
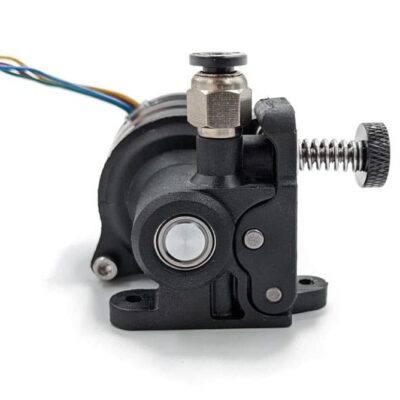
It’s an open-source extruder made by Robert Lorincz and it weighs only 140g which is quite impressive. If you haven’t heard about the Orbiter extruder, I don’t really blame you. The Trianglelab Matrix Extruder can be purchased from the following websites: You will be able to improve print quality without compromising on the maximum speed you can achieve with your printer. For example, I would choose this for an Artillery Sidewinder X1, Genius, or a Creality CR-10. I recommend getting the Trianglelabs Matrix for large format 3D printers who already have a quite heavy heatbed. Even so, don’t let the weight deter you from grabbing one if you like it. It’s one of the best direct drive extruders available right now, but it’s also one of the heaviest. I previously reviewed the Trianglelabs Matrix and it performed really well. This makes the thermal performance a bit better while also requiring less airflow. The main difference between the Matrix and the Hemera is the use of a bi-metal heat break instead of the regular titanium heat break used on the Hemera.
#Orbiter extruder wiring upgrade#
This will make the Trianglelab Matrix an easy upgrade because of the huge selection of mounts and fan ducts available. It’s cooled by a 4010 fan and it maintains compatibility with all the designs made for the Hemera. The heatsink has a different design, but otherwise it looks remarkably similar. The Trianglelabs Matrix has a big resemblance of the E3D Hemera. With a bowden setup, you will be severely limited by the speed you can print these materials, and on some printers it’s not even possible.Ī lot of people upgrade to a direct drive extruder specifically for printing flexibles faster and with better quality.

Even so, regular speeds of about 60mm/s should be easily achieved without much ringing.Īnother benefit of running a direct drive extruder is the possibility of printing flexible filaments, like TPU, TPE, Ninjaflex and others. Because the motor is next to the hotend and it moves during printing, you won’t be able to push speeds as high as with a bowden setup. There’s also a drawback for direct drive extruders and that’s weight. Retraction will be much lower compared to a bowden setup, and you can even set it to 0 with some direct drive extruders and proper calibration of linear advance/pressure advance. Because the filament path from the extruder to the nozzle is much shorter compared to a bowden setup, you will be able to tune your extrusion much easier. The main reason to buy a direct drive extruder is to have better control of your filament. I notice you used Version 2 of the hub housing.5 Wrapping Up Why buy a Direct Drive Extruder? How do you think it works compared to versions 3 and 4 that use a heat break as a filament guide? I notice you used Version 2 of the hub housing. (In the photo the part on the left is in PLA-CF and the grear set and spider/drive shaft is in nylonX) BTW, I was able to use a 0.4mm nozzle with the extrusion size set to 0.2 mm (in Simplif圓d) and 0.1 layer height and have parts that look almost layerless.
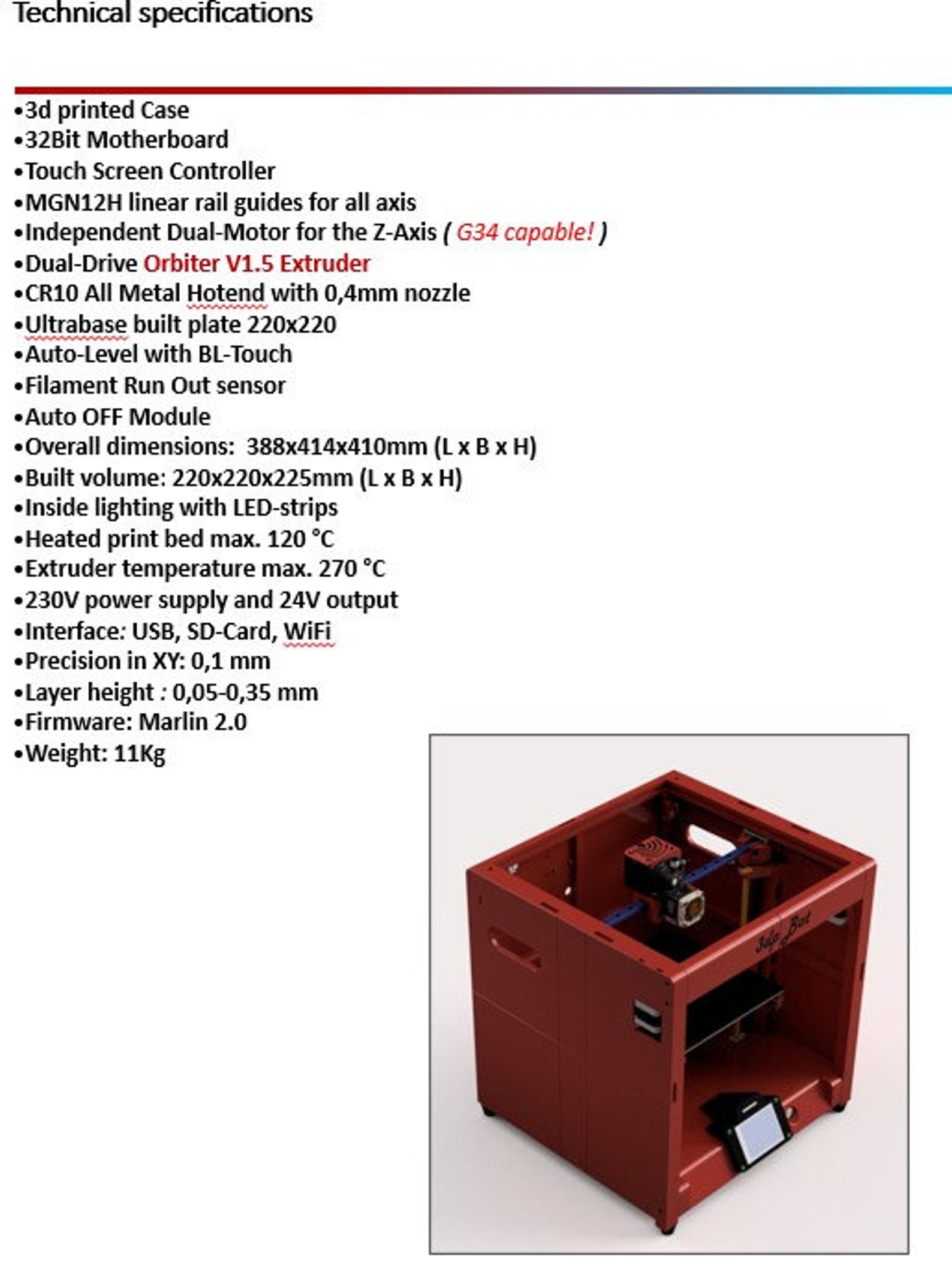
So far, I have parts which I have stressed in a drill press ( I put the drive shaft in the chuck and run them for about 30 minutes at a slow "wood drilling" speed to break them in since the nylonX doesn't print with the highest level of detail) but have not put them into actual use yet. The modification changes the spider pins and spur gears so that they can be press it together after being heavily lubricated (eliminating the 3 small ball bearings). I have a modification that I made if you print the gears, hub, and combined spider and drive shaft in nylon (I am using nylonX from Matterhackers.
